Dual-Pole Reed Relays
A dual-pole (a.k.a. double-pole or 2-pole) reed relay comprises two reed switches that are operated by a single coil. The switches are either both single throw, normally open (i.e. Form A) or double throw (i.e., Form C).
Note, double pole single throw normally closed (Form B) reed relays are not usually offered as a catalogue device but can always be built as a custom device.
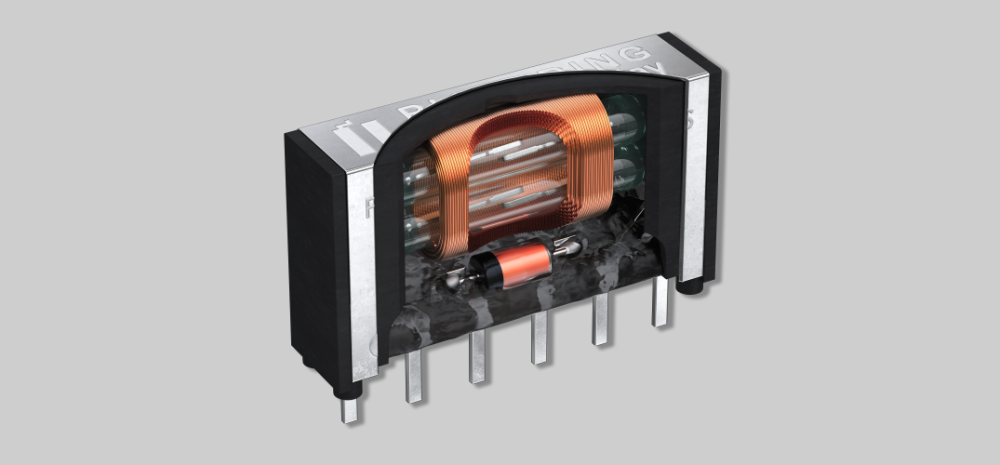
With two switches present (see figure 1), device denotation is:
- 2 Form A = double pole, single throw (normally open).
- Switches horizontal in the package
- Switches vertical in the package.
- 2 Form C = double pole, double throw.

Figure 1 – On the left, a dual-pole-single throw, normally open (2 Form A) reed relay with the switches horizontal and in the middle image with the switches vertical in the package, ideal for switching two circuits at approximately the same time. On the right, a dual-pole double-throw (2 Form C) reed relay, ideal for implementing a cross-over function in a circuit.
Benefits & Applications
The main advantage of a double-pole reed relay is that it takes up less space on a PCB than two single pole relays with their coils connected in parallel. It must be stressed though that despite the common coil, the switches will not operate at exactly the same time, but still within their operational parameters. Placing the switches in parallel as a means of doubling the power is not advised for ‘hot switching’.
Applications
These include, but are not limited to:
- In test and measurement applications where Kelvin or 4-wire test point connections are required, a double-pole reed relay can be used to connect a source signal and a sense (measurement) line at approximately the same time.
- For high power cold switching applications, connecting the switches in parallel can double the carry current capability (compared to a single pole device with the same switch rating) for both continuous and pulsed operation.
- In data acquisition, where a very low signal needs to be switched with minimal risk of being influenced by thermal EMF, a double-pole reed relay can be used with the switches connected with opposing polarities – i.e. the current through one switch is in the opposite direction to the current flowing through its neighboring switch. This cancelling effect can result in a much lower overall thermal EMF when compared to a similar sized single pole device.
- Connecting both switches in parallel can also halve the contact resistance, which can be important in some applications; the detection/measurement of extremely small voltages or currents, for example.
- In applications where a single signal may need to be switched to two separate paths. This is done by making the source sides of both switches common.
- Double-throw dual-pole reed relays can be used for redirecting the path of a complementary pair signal, i.e. a single signal that has composite parts (a positive and a negative element) that are not referenced to ground. LVDS is a prime example.
- To extend contact life when hot switching high power. When connecting two switches in parallel, and because the switches will not close at exactly the same time, one will hot switch the load and take the switching current; and any surge. When the second switch closes it will take half the carry current. The overall contact resistance is also halved. The switch that is hot switching may degrade over time, but the second will retain its contact performance and stability for billions of operations. Note: this technique is a good way of reproducing some of the performance characteristics of a mercury switch, i.e. the ability to handle a high carry current and to lower the contact resistance.
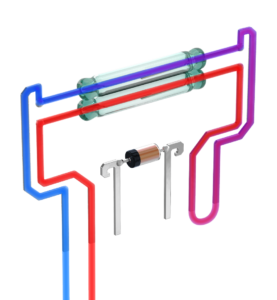
A double-pole reed relay with the switches connected with opposing polarities, causing a cancelling effect for extremely low thermal EMF applications.
Construction
There are a number of ways in which the two switches might be orientated. If they are horizontal, with one switch above the other, a double-pole device will be between 30 and 50% taller than a single-pole device employing the same switch. In most cases, the footprints of the double- and single-pole devices are usually the same, so if PCB space/area is at a premium – and component skyline (height) is a secondary consideration – the horizontal stack makes sense.
Where high density is desired, some devices have their switches vertically orientated in which case the footprint is also 30 to 50% larger, and the height is increased.
In all cases, irrespective of the orientation and positioning of the switches, the footprint of a double-pole reed relay will be less than the combined footprints of two single-pole devices.
Benefit: Irrespective of the orientation and positioning of the switches, double-pole reed relays take up less space than two single-pole devices.
Coil Resistance
The coil resistances for double-pole reed relays are often lower than the comparable single-pole device, more so for smaller, higher density packages. With two reed switches in the same coil, more magnetic field is required to operate both compared to a single switch. However, in general, the coil resistance of a double-pole device will be greater than two single-pole devices with their coils in parallel.
Benefit: Double-pole reed relays are ideal for applications that have tight power budgets and require cross-over or approximately coincidental switching.
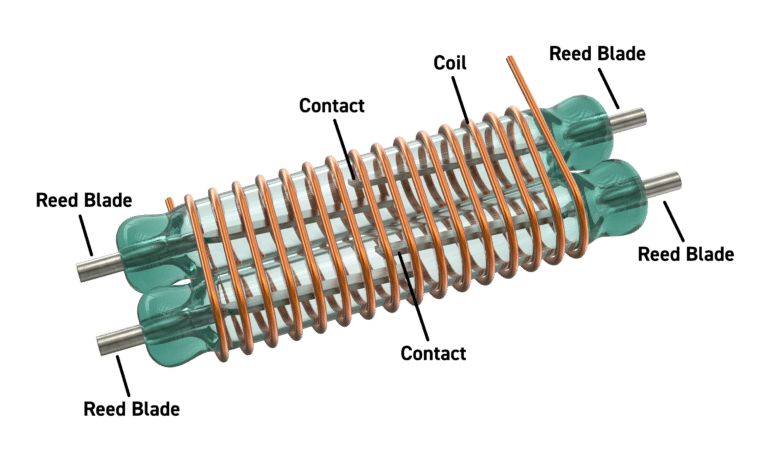
Contact Resistance
The lead frame of a double-pole reed relay can be larger than that of a single-pole device, which can make for a longer switch path and therefore a higher overall contact resistance; between 10 and 20% higher. However, where this is the case, Pickering mitigates against this by increasing the lead-frame’s cross-sectional area. The company also engineers the lead frame such that the two switching paths have similar contact resistance.
Benefit: Double-pole reed relays with instrumentation grade switches can be used in the same sort of applications (data acquisition, for example) as their single-pole counterparts.
Noise
Above, we outlined the many benefits of double-pole reed relays. We also want to draw your attention to an effect that might be an issue for some (but far from all) applications. As mentioned, the two switches do not operate at exactly the same time. When closing it is possible for the second switch to close to induce noise (a ‘blip’) onto the already closed switch. This is because the completed metal path (of the second switch to close) momentarily disrupts the magnetic field.Life Expectancy
Because the same reed switch type will be used in the double-pole reed relay as its single pole counterpart, the expected life will be the same. If used within its intended operating parameters, a double-pole reed relay can perform billions of operations with little if any degradation in performance. For further information see ‘Understanding Reed Relay Life Expectancy’.Pinouts
Many of Pickering’s reed relays are available in both single- and dual-pole versions, and this is certainly the case for the majority of the company’s SIL packaged parts.
Understandably, a dual-pole device has more pins than its single-pole equivalent, i.e. a 1 Form A has fours pins, whereas a 2 Form A has six. Similarly, a 1 Form C has five pins and a 2 Form C has eight.
Where possible, Pickering tries to keep the pins that are common to the single- and dual-pole devices (in any given range) in the same position, making them multipurpose. Specifically, customers can design their PCBs to accept both versions.
Recommended Dual Pole Reed Relays
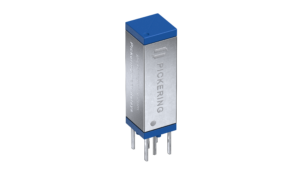
Series 125 Ultra-High Density
The smallest 2-pole reed relay in the world. The Series 125 delivers 20W, 1A switching and has an optional internal diode.
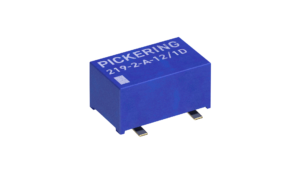
Series 219 HV SMD
Pickering's High Voltage SMD 2-pole reed relay delivers up to 1kV switching with up to 1.5kV standoff, all in a compact package.
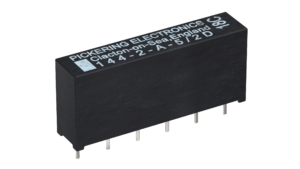
Series 144 High Power
The Series 144 is Pickering's highest power mini SIP reed relay, offering up to 80W switching at 1A, or 60W at 2A.
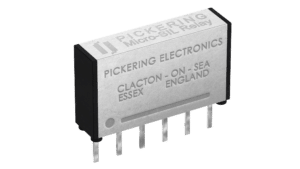
Series 109 Micro-SIL
Very small 2-pole relays at just 3.7 x 15.1 x 8.9mm. Fantastic for low-level switching. Full mu-metal package for high packing density with minimal magnetic interaction.
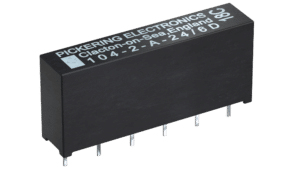
Series 104 Mini SIL up to 2kV
The Series 104 2-pole reed relays offer up to 1kV switching and up to 2kV standoff, ideal for a wide range of applications.